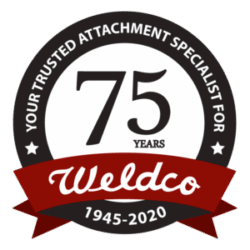
In 1945, Gordon Reelie founded Weldco in post-war Vancouver, on a prime downtown spot on 2nd Avenue. From a humble welding shop whose name said it all (welding + company = Weldco) came the impressive corporation we know today that designs and manufactures specialized heavy equipment attachments for OEMs and their Dealers.
Weldco expanded to Edmonton in the early 1970s, and in the 1980s, officially named Edmonton as its head office and merged with Beales Steel Products. The Vancouver operation eventually moved to Langley in 1991, and the next expansion was in Barrie, Ontario in 2006.
Although our roots were set in the growing forestry sector of British Columbia, we began to offer heavy equipment dealers specialized attachments in the construction, resource, mining, scrap recycling and road maintenance industries, spanning across North American, Europe, Asia and South America. Additionally, we are the only Canadian manufacturer of truck-mounted cranes, competing with some of the largest crane manufacturers in the world while earning market share leadership in Western Canada.
Product Innovation
A high level of engineering and design goes into our product mix. Tolerances have become significantly tighter as the equipment our attachments work with has evolved over the years, which works well for us, as we have built our reputation on providing in-house, engineered solutions. Our dedicated engineering teams at all manufacturing facilities ensures that we continue to meet and exceed regional design expectations.
We are in the business of making our customers more successful. We appreciate and respect the trust of our customers who depend on our products, services and technology to add value to their business. The significant investments we’ve made in smart technology, manufacturing processes, raw material sourcing, engineering and new product development have allowed us to stay competitive in a very demanding industry.
Weldco has also been extremely fortunate to work with such amazing suppliers and service providers; they play an integral role in the daily operations of all our branches. Not only have we seen the long-term benefits of investing in partnerships with key suppliers, but we owe much of our continued success to maintaining these important relationships.
Community Focused
Weldco continues to make a difference in the communities we serve and we support many organizations including but never limited to: the United Way, NAIT, the Canadian Centre for Welding & Joining, YMCA, Big Brothers Big Sisters of Canada, Cystic Fibrosis Canada, CURE Foundation, Prostate Cancer Canada, Children’s Aid Society, local Food Banks, and The Terry Fox Foundation.
Weldco Companies is also a proud member of the Inuvialuit Development Corporation (IDC). This organization represents the Inuvialuit of the North West Arctic and is a 100% Inuvialuit-owned for-profit holding company. IDC has cultivated a diversified, growth-oriented portfolio as the business arm of the Inuvialuit Regional Corporation (IRC). Weldco is committed to giving the Inuvialuit beneficiaries access to employment opportunities.
Future Focused
In addition to being ISO 9001:2015 certified in the Edmonton branch, which speaks to the commitment we have made to quality and safety across our brands, our management team is committed to best practices to protect our staff and our customers.
We work together to build a culture that empowers our team and focuses on results. This strong culture is rooted in safety and is the backbone to our success. Our famous quote: “We will conduct our business on the principle that our work is never so urgent or important that we cannot take time to do it safety,” speaks volumes in our continuous commitment to our employees.
Each team member trusts in one another and everyone challenges each other to be better, knowing that everyone plays a critical role in the future success of Weldco regardless of position or title. Understanding the needs of customers and the values of the team have been the key to Weldco’s 75 years of success.